Höhe halten – Gurit
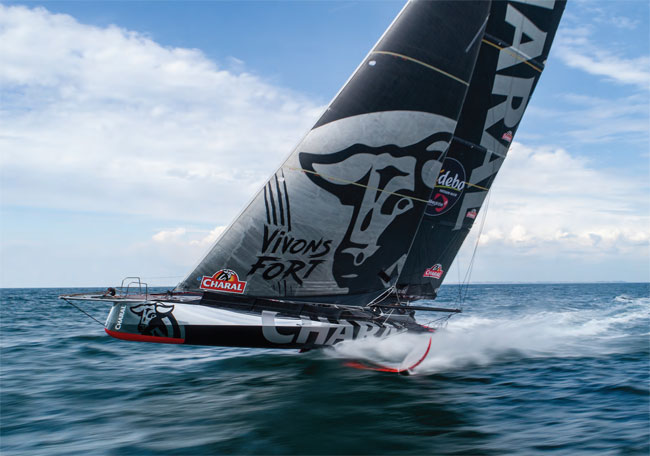
Abheben… ankreuzen. Intermittierender Flug… Tick. Stetiger Flug über Wellen und Ozeane… die Lasten sind fast außer Kontrolle. Doch mit Hilfe einer brillanten Composite-Technik passiert es
Seit den ersten atemberaubenden Bildern von Jeremie Beyous Charal im Flug gibt es nun viele Beweise dafür, dass diese beeindruckende Präsentation kein einmaliges Partystück war. Für viele in der Imoca 60-Flotte ist es jetzt die neue Norm, mit einem sieben Tonnen schweren 60-Fuß-Boot vor der Küste zu fliegen, das mit weit über 20 Knoten in Wellen fährt, während es auf einem riesigen Foil in Lee und einer Finne zum Wetter balanciert ist. Kein Wunder also, dass Composite-Experten
Gurit hat bereits mehr als 6,000 Stunden für die verschiedenen Imoca 60-Projekte aufgewendet, an denen sie seit der letzten Vendée Globe beteiligt sind. Selten war es so wichtig, eine Struktur zu entwickeln, die solch extremen Leistungen standhält. Gurit Composite Engineering arbeitet seit über 60 Jahren eng mit Imoca 20s zusammen. Seit Ellen MacArthurs berühmter Kingfisher, die in Zusammenarbeit mit Humphreys Yacht Design und Owen/Clarke entwickelt wurde, hat das Unternehmen beträchtliche Erfahrungen auf diesem Gebiet gesammelt, die zu sieben der acht neuen Boote der diesjährigen Vendée Globe-Flotte mit Gurit-Materialien beigetragen haben, während 12 Kampagnen haben Gurit-Ingenieure für Aspekte ihres Engineerings engagiert. Von den neuen Booten in der Flotte, Charal, Hugo Boss und dmg mori tragen die Handschrift von Gurit Structural Engineering in Zusammenarbeit mit VPLP Yachtdesign.
Auch der Zeitaufwand für einzelne Projekte ist gestiegen.
„Im Vergleich zum vorherigen Zyklus ist die Zeit, die wir für diese Iteration von Vendée-Projekten aufgewendet haben, um mindestens 50 Prozent gestiegen“, sagt Paolo Manganelli, Chefingenieur von Gurit. "Da sich die Teams mehr darauf konzentrieren, einen Leistungsvorteil zu finden, verbringen wir mehr Zeit in der Anfangsphase des Projekts, in der wir an verschiedenen Designkonzepten und Optionen arbeiten, um diese Leistungssteigerungen zu ermöglichen."
In den letzten 20 Jahren sind die Durchschnittsgeschwindigkeiten weltweit um rund 30 Prozent, die Höchstgeschwindigkeiten um rund 50 Prozent gestiegen, während die Strukturen leichter geworden sind. Und während der Leistungsdruck weitergeht, ist die aktuelle Ernte in der Lage, einen Balanceakt wie kein anderer zu vollführen, die Gesetze der Physik in Frage zu stellen und konventionelle Vorstellungen davon zu überwinden, wie es ist, ein Rennboot zu segeln.
Ähnliche Beispiele anderswo sind selten, abgesehen vom America's Cup, der die Foiling-Angriffe anführte und in kurzer Zeit enorme Leistungssprünge verzeichnete. Wie sehr hat der Cup den neuen Look der Imoca 60s beeinflusst oder beeinflusst?
„Der Cup hat sicherlich dazu beigetragen, Werkzeuge und Konstruktionsverfahren zu entwickeln, um das Verhalten des Bootes und damit die Simulation der Lasten vorherzusagen“, sagt Manganelli. „Das war ein großer Beitrag. Darüber hinaus wurde durch die im Cup durchgeführten Arbeiten auch die Fähigkeit, die Fluglage der Boote vorherzusagen, verbessert.
„Aber obwohl es Ähnlichkeiten und Verbindungen zwischen den beiden Gebieten gibt, kehren Cup-Boote jeden Tag zum Dock zurück und haben Verfolgungsboote in der Nähe. Eine Imoca 60 ist möglicherweise erst einen Monat oder länger zurück, daher stehen wir vor ganz anderen Herausforderungen, wenn es um die Art und Weise geht, wie diese Boote in ihrer normalen Umgebung funktionieren.'
Für Imoca 60s ist es eine Sache, das Boot aus dem Wasser zu heben, aber die Auswirkungen auf Design, Technik und Konstruktion haben anderswo erhebliche Veränderungen erfahren, die eine viel engere Zusammenarbeit zwischen Designern, Bauherren und Materiallieferanten als je zuvor erfordert haben.
„Die Einführung von Foils hat die Lastbedingungen verändert, da das Leefoil mit der Flosse des Canting-Kiels zusammenarbeitet, um das Boot mit Geschwindigkeit anzuheben“, erklärt Manganelli. „Wir müssen uns also nicht nur mit der Stützstruktur des Foils selbst befassen, sondern wir müssen jetzt auch die zusätzlichen Lasten berücksichtigen, die in die Bootsstruktur eingebracht werden.
„Die Struktur um die Folie herum ist ziemlich komplex und einige der Konstruktionslasten liegen in der gleichen Größenordnung wie die des Kiels. Tatsächlich haben wir also ein zusätzliches aufrichtendes Moment hinzugefügt, das ein Anhängsel erzeugt, das dem Boot einen großen zusätzlichen Moment verleiht. Das Ergebnis ist, dass Sie ein zweites wichtiges Strukturelement in ähnlicher Größenordnung wie der Kiel zu bewältigen haben und dennoch das Gewicht der Kieltragstruktur bei diesen Booten nicht wirklich verdoppeln. Stattdessen integrieren wir die Foil-Tragstruktur in die Kiel-Tragstruktur, sodass einige der Elemente einen doppelten Zweck erfüllen, um den Booten keine zusätzliche Masse zu verleihen.“
„Auch die Struktur an anderen Stellen im Boot hat sich weiterentwickelt, da wir mehrere zusätzliche Herausforderungen zu bewältigen haben. Für den Fall, dass die Foils zum Beispiel auf etwas treffen, müssen wir sicherstellen, dass das Boot nicht in Stücke gerissen wird. Die Hugo Boss Kollision bei der Transat Jacques Vabre im letzten Jahr ist ein gutes Beispiel dafür, dass das Boot ernsthaft beschädigt wurde, aber es wieder an Land schaffte.
„Um dies zu erreichen, nutzen wir die Erfahrung, die wir bei einer Reihe von Konstruktionen von Tragkonstruktionen aus Folien für Projekte mit Maxis, Imoca 60s, Volvo Ocean Race-Booten und anderen gesammelt haben. Es ist also eine komplexe Designherausforderung, aber es ist keine unbekannte.'
Aber das ist nicht das Ende des Themas. So wie sich die Änderung der Leistungsentfaltung in einem Auto auf verschiedene andere Bereiche von Getriebe, Bremsen, Fahrwerk usw.
„Bei dieser letzten Generation, der Kombination aus Ballasttanks, Kippkiel und Rake-Einstellung an den Foils, gibt es so viel zu optimieren und zu lernen und einzustellen und so viele Parameter; es ist eine ständige und rasante Entwicklung. Betrachtet man den Leistungsverlauf von Charal Von ihrer Markteinführung bis heute ist die Verbesserung ziemlich außergewöhnlich, wie es bei anderen in der Flotte der Fall war. Es gab bereits einen gewissen Unterschied zwischen der Leistung, die von dem Boot in der Entwurfsphase erwartet wurde, und der Leistung, die es beim Segeln tatsächlich erbrachte. Und dann gab es einen weiteren Schritt vorwärts zwischen dem, was sie vor anderthalb Jahren tat, und dem, wozu sie jetzt fähig ist. Unterm Strich war das Tempo der Veränderungen unglaublich schnell und die Lernkurve steil. Die Herausforderung für uns besteht also darin, dieser Kurve einen Schritt voraus zu sein. Die enge Zusammenarbeit mit Teams macht dies möglich.
„Mit zunehmender Leistung ist das Slamming ein weiterer kritischer Bereich. Während Corecell zum Material der Wahl für den Kern in der Unterseite des Rumpfes geworden ist, konnten wir seine Nutzung dank des verbesserten Verständnisses seines dynamischen Verhaltens weiter optimieren. In den letzten Jahren haben wir durch umfangreiche Tests, die von unserem neuseeländischen Büro in Zusammenarbeit mit der University of Auckland durchgeführt wurden, äußerst wertvolle Einblicke in die Eigenschaften von Corecell bei hohen Dehnungsraten gewonnen. Ein Teil dieses Wissens ist in unsere Designs eingeflossen. Eine enge Zusammenarbeit mit den Teams ist der Schlüssel, um unser Verständnis der neuen Ladekonfigurationen, denen diese Boote ausgesetzt sind, weiter zu verbessern. '
Im Umgang mit vielen der weltweit führenden Unternehmen, darunter Unternehmen wie CDK Technologies und Carrington Boats, die viele der extremsten Offshore-Maschinen hergestellt haben, sowie jüngere Unternehmen wie Black Pepper Yachts, die Armel Tripons radikal aussehende L'Occitane gebaut haben Provence, der technische Verkaufsleiter von Gurit, Yannick Le Morvan, sieht dies aus erster Hand.
„Zusammenarbeit ist der Schlüssel, um diese Projekte voranzubringen“, sagt er. „Die Detailtreue, mit der die modernen Designs erstellt werden, bedeutet, dass die gesamte Übung eher eine Zusammenarbeit als die vorherige Beziehung ist, bei der die Partner möglicherweise einfach Materialien und/oder Daten geliefert haben. Ein gutes Beispiel dafür, wie dies in der Praxis funktioniert, ist der Aufbau eines Laminats und die genaue Verlegung der Fasern.
„Für einen bestimmten Bereich bauen wir jetzt mehr Schichten ein, die dünner und präziser angeordnet sind, um die besten strukturellen Eigenschaften zu erzielen. Wo wir in der Vergangenheit vielleicht 300g/m² verwendet haben2 Faser bei 0° und sagen wir 90°, besteht nun ein Großteil des Laminats aus 150-Gramm-Lagen, die in mehrere Richtungen gelegt werden. Dies bedeutet, dass der Layup-Prozess genauer sein muss, was wiederum mehr Zeit in Anspruch nimmt und in einigen Fällen einen etwas anderen Ansatz erfordert. Der Debulking-Prozess ist auch komplizierter, da Sie die Luft zwischen jeder Lage herauslassen müssen.
„Die raffiniertere Beschaffenheit der Laminate hat auch Auswirkungen auf die Härtungszyklen, die oft komplexer sind und bei denen Sie mehr über die Materialwissenschaften wissen müssen, um die beste Struktur zu erzielen.
"Angesichts dieser und anderer Faktoren war es großartig, mit CDK-Technologien zu arbeiten, da diese Art von Partnerschaft dazu beiträgt, diese Projekte voranzutreiben."
Nicht jedes Team im aktuellen Vendée Globe-Zyklus hatte den Luxus, seine Projekte von einer leeren Leinwand aus zu beginnen. Für Teams wie die von Isabelle Joschke MACSF und Boris Herrmanns Meeresforscher (beide profitierten von der Zusammenarbeit zwischen Gurit Structural Engineering und VPLP) erforderte die Aufrüstung eines Designs der vorherigen Generation, um modernes Foliendenken zu akzeptieren, an einigen Stellen einen subtil anderen Ansatz. Diese Boote wurden ursprünglich nicht mit Blick auf das aktuelle Foiling-Niveau entworfen, was es schwieriger macht, eine ausreichende Struktur zur Aufnahme der neuen Lasten von den Foils ohne Erhöhung des Gesamtgewichts aufzunehmen.
„In diesen Fällen müssen Sie nicht nur eine ausreichende Stützstruktur für die Foils bereitstellen, sondern auch sicherstellen, dass Sie keine bestehende Struktur an anderer Stelle im Boot brechen“, sagt Manganelli. „Sie müssen ein Layout umgehen, das nicht wirklich für diese Foliengröße und -position optimiert wurde, und Sie müssen auch die zunehmenden Lasten berücksichtigen, die an anderer Stelle übertragen werden. Wenn die Boote schneller fahren, werden sie außerdem härter zuschlagen, und so haben viele Boote der früheren Generation ihre Rumpfschalen durch das Anbringen neuer Foils verstärkt.'
Weitere Informationen zu Gurit finden Sie hier »
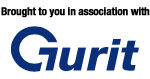
Dieser Artikel wurde ursprünglich im Seahorse Magazine veröffentlicht und wird freundlicherweise mit deren Erlaubnis reproduziert. Um ihr Archiv der frei einsehbaren Artikel zu überprüfen, besuchen Sie bitte https://seahorsemagazine.com/archive/2020-archives
Um Seahorse zu einem ermäßigten Preis zu abonnieren, klicken Sie bitte hier: http://bit.ly/SHMIN20
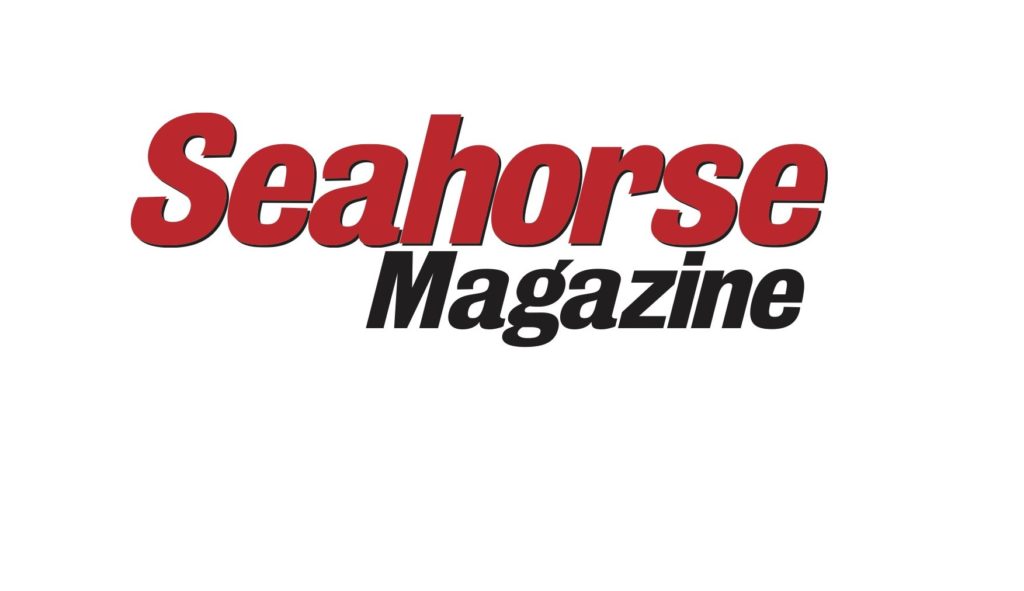